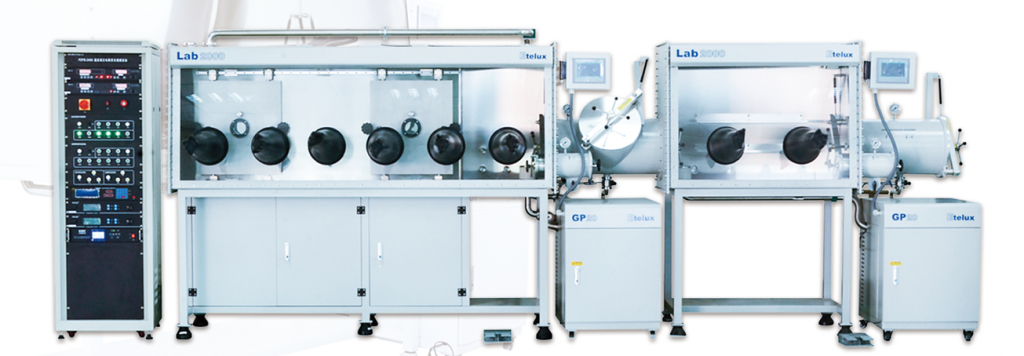
Vacuum evaporation coating is one of the most commonly used methods for deposition of functional films on to various substrates. The vacuum is used to allow vapor particles to deposit directly on to the substrate, where vapor particles condense back to a solid state, forming a functional coating.
The vacuum evaporation coating process involves two basic stages: the evaporation of a functional material and the condensation on the substrate. In high-vacuum evaporation, electrical heating or electron beam heating is used to melt, gasify and evaporate the coating materials. The vapor of the coating material then travels to the surface of the substrate and gradually cools, a thin film layer of good quality is finally formed (Jankowski and Hayes, 2004).
Vacuum is used to prevent the collision of the evaporated particles with the background gas or other unwanted particles. Evaporated functional materials deposit on to the surface of the substrate.
Etelux offers a vacuum deposition system that is a combination of a vacuum deposition system and a vacuum glove box system. Thin film evaporation can be accomplished in the high vacuum evaporation chamber, and sample storage, preparation, and testing of evaporated samples can be performed in the glove box under high purity inert gas atmosphere. The combination of evaporation coating and vacuum glove box realizes the fully enclosed production of evaporation, encapsulation, testing and other processes. The entire film growth and device preparation process is highly integrated in a complete system of controlled environmental atmosphere, which can eliminate the influence of unstable factors in the atmospheric environment during the preparation of large-area circuits. This guarantees the preparation of high-performance, large-area organic optoelectronic devices and circuits.
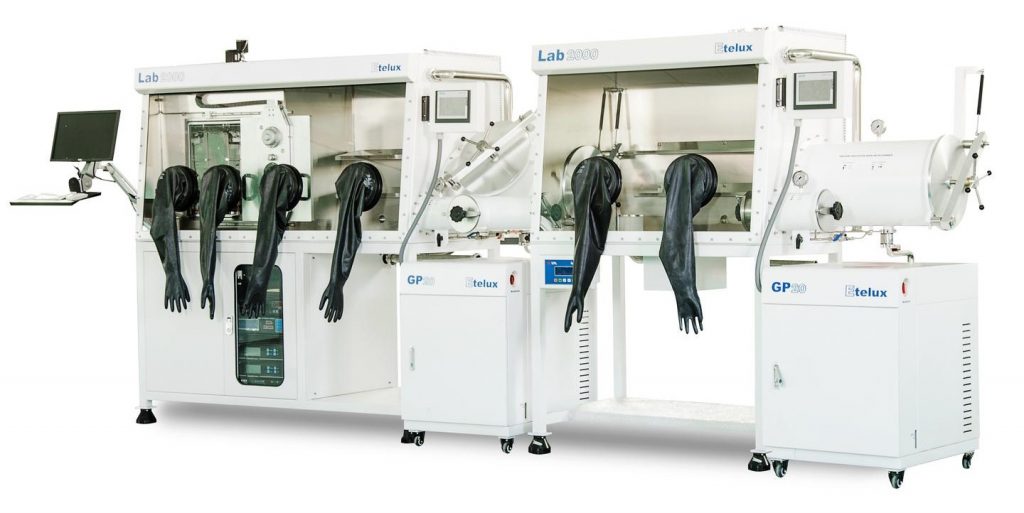
Vacuum Coating Glove Box is a complete and directly usable standard vacuum equipment, which is combined by the main chamber, main transition chamber, tool transition chamber, vacuum extraction system and various parts. It is characterized by high airtightness, long pressure holding time, simple operation, etc. It can meet the application of scientific research in institutions and small batch production.
The glove box is designed for closed circulation to save running cost. Under standard conditions, i.e. 20ºC constant temperature, one standard atmospheric pressure, 99.999% inert gas source, water and oxygen content of less than 1 ppm. Box and transition chamber is made of 304 stainless steel plate. The front window is tempered glass, wear-resistant and corrosion-resistant.
Touch screen PLC control, high degree of automation. Glove box can realize: automatic control of gas pressure in the box, automatic cleaning of the atmosphere in the box, automatic regeneration of purification data, automatic recording of system operation data and other operations.
Application
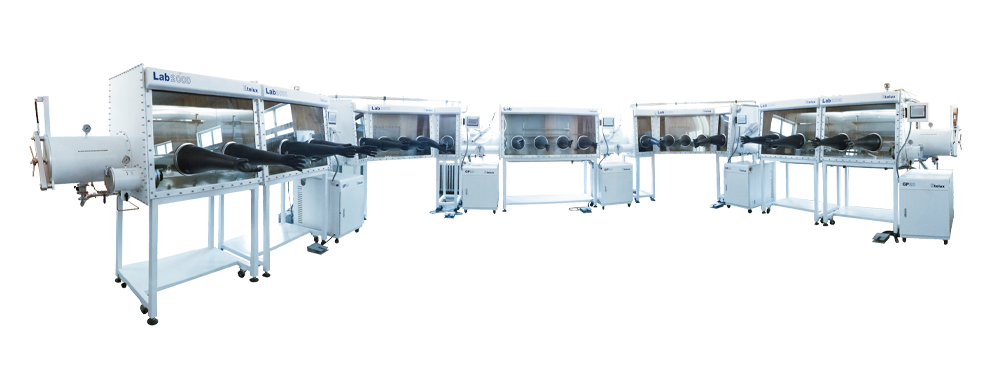
1. Electronics.
Nearly 50 percent of all large-scale integrated circuit processes are tied to vacuum equipment. For ultra-large-scale integrated circuits is even larger, the required vacuum process and equipment to occupy about three-quarters of as much. Applied in the field of electronics, the existence of vacuum coating technology to ensure a high degree of integration of integrated circuits, performance, reliability, production efficiency.
2. Superconducting technology industry.
Application in the superconducting technology industry, common examples of coating are high purity Nb superconducting sputtering film, InSb amorphous superconducting film, V-Hf-Zr system superconducting film.
3. Aerospace field.
Equipment in the aerospace field is required to withstand high temperatures, radiation irradiation, and ultra-high vacuum environments. For equipment working in this environment, liquid lubricants are no longer effective. In the face of unavoidable high temperature, friction, wear, abrasion, oxidation, cavitation, corrosion, leakage and other factors, solid lubrication film is essential.
Aerospace equipment involved in a variety of screws, gears, bearings, instruments and other commonly used vacuum evaporation coating, sputtering coating, ion coating and other processes coated with film. For example, high-temperature turbine engines, sputtering Co-Cr-Al-Y alloy coating on its blades, can significantly improve the engine corrosion resistance, oxidation resistance, high temperature performance.
4. New Energy Field.
Various structures of thin film solar cells, such as amorphous silicon, II-IV (such as Cds-Cu₂S), III-V (such as CaAs) and other thin film solar cells.
5. Mechanical Realm.
Vacuum coating technology in the field of machinery manufacturing, tool coating is a wide range of typical applications. Tool coating is mainly TiC, TiN and its composite coating, in addition to Al₂O₃ and so on. The thickness of the coating is usually between 2µm and 10µm. Ordinary tools such as knives, drills, taps, etc. can be coated with TiN to increase productivity and cutting speed. For molds, measuring tools, precision equipment shafts, wear-resistant devices can extend the service life of the machinery through the treatment of wear-resistant coatings (e.g., TiC, etc.).
7. Laboratory Coating.
Aluminum coating on the surface of reactor fuel elements by ion plating can achieve the effect of corrosion prevention. Some low atomic number and high melting point materials (such as TiB₂, B₃C, TiC, etc.) in controlled thermonuclear reactors can be formed to provide surface protection, high-temperature protection, and so on.
If you have any questions, please contact Etelux.